The Evolution of Continuous Improvement: A Blueprint for Modern Business Leaders
As the contemporary landscape of hospitality evolves continuous improvement has become a cornerstone for achieving sustained success. But where did this transformative philosophy begin, and how has it evolved over time to become a critical strategy for today's senior business leaders?
The Origins: A Japanese Revelation
The journey of continuous improvement, often referred to as "Kaizen" in its earliest form, can be traced back to post-World War II Japan. Faced with the daunting task of rebuilding its economy, Japanese industries embraced a philosophy that prioritized incremental, ongoing enhancement over radical change. This approach was championed by influential figures such as W. Edwards Deming and Taiichi Ohno, who introduced statistical quality control and the Toyota Production System, respectively. Their pioneering work laid the groundwork for what would become a global movement.
The Western Adoption: Quality Circles and Beyond
As Japan's economy flourished, the Western world took notice. By the 1980s, concepts such as Total Quality Management (TQM) and Six Sigma began to gain traction in the United States and Europe. Companies like Motorola and General Electric were early adopters, leveraging these methodologies to drive efficiency, reduce defects, and enhance customer satisfaction. The success of these initiatives highlighted the potential of continuous improvement to deliver measurable, impactful results.
The Digital Revolution: Agile and Lean
The advent of the digital age ushered in a new era for continuous improvement. The rise of Agile methodologies in software development emphasized flexibility, collaboration, and rapid iteration. At the same time, Lean principles, derived from the Toyota Production System, were being applied across various industries to minimize waste and maximize value. This fusion of Agile and Lean created a powerful framework for continuous improvement that could be adapted to diverse business contexts.
Continuous Improvement Today: A Strategic Imperative
Today, continuous improvement is not just a set of tools or techniques; it is a strategic imperative for organizations seeking to thrive in a competitive environment. Senior business leaders must foster a culture that encourages experimentation, values feedback, and prioritizes learning. This mindset enables organizations to adapt to market changes, innovate, and achieve long-term resilience.
The Future: AI and Beyond
As we look to the future, the integration of machine learning and AI presents exciting opportunities for continuous improvement. Predictive analytics, automated workflows, and real-time data insights can drive even greater efficiencies and uncover new areas for enhancement. Forward-thinking leaders will harness these technologies to stay ahead of the curve and maintain a relentless focus on improvement.
By understanding the history and evolution of continuous improvement, business leaders can better appreciate its significance and leverage its principles to drive their organizations toward enduring success. Embracing a culture of continuous improvement is not just a business strategy—it's a commitment to excellence that will define the successful businesses of tomorrow.
Understand Yumpingo's Continuous Actions Process
Acronyms and Terminology: What do all these things mean?
There are a lot of terms, theories and methodologies that get wrapped up in the ideas of continuous improvement. Here is more background on the key terms mentioned above:
Continuous Improvement
Continuous improvement is the ongoing process of analyzing performance, identifying opportunities, and making numerous incremental changes that add up to significant results.
By utilizing real-time feedback to optimize offerings and processes, businesses deliver a better overall experience, increasing guest satisfaction and delivering substantial revenue growth.
The ethos behind continuous improvement is that no process is perfect and there is always room for improvement. Continuous improvement isn’t reaching perfection; it’s about striving for progress, whether you’re fine-tuning a process or revolutionizing your approach.
Kaizen
Kaizen is a Japanese term meaning changes for the better, or continuous improvement. It was a set of ideas developed in the automotive industry at a time when Japan was building its reputation for high quality manufacturing, mechanical reliability and competitive value, that enabled them to become the dominant global force in car production. It is a business philosophy that focuses on continuously improving operations and it involves all employees.
Total Quality Management (TQM)
Total quality management is a continuous improvement approach that increases customer satisfaction and employee involvement. By having everyone contribute to improving quality, companies reduce errors and improve essential processes to improve quality.
Total quality management is an organization-wide effort to “install and make permanent a climate where employees continuously improve their ability to provide on demand products and services that customers will find of particular value." - Ciampa, Dan (1992). Total Quality: A User's Guide for Implementation
Under TQM, your customers define whether your products are high quality. Increased quality is an ongoing process of detecting and reducing or eliminating errors. Quality improvement is a continuous effort and conducted throughout the organization.
Incremental Gains (or Incremental Improvement)
Incremental gains is an approach to process improvement in which your team focuses efforts on smaller solutions that slowly but surely move the business toward success. These ideas are typically low-cost and low-risk, and are implemented by employees throughout the entire organization. The most famous example is how the British cycling team used these techniques to start dominating Olympic cycling and we wrote about that here.
Agile Methodology
Agile project management is an iterative approach to managing development projects that focuses on breaking the project into phases (known as sprints), continuous releases and incorporating customer feedback with every iteration.
Commonly used in software development, teams follow a cycle of planning, executing, and evaluating (our Product and Engineering teams operate this way at Yumpingo). Teams that embrace agile project management methodologies increase their development speed, expand collaboration, and foster the ability to better respond to market trends and customer needs.
Lean Thinking
Lean thinking is a systematic approach aimed at optimizing efficiency and eliminating waste in various processes. It originated from the Toyota Production System otherwise known as the Just-in-Time system. Its core principles and elements are:
- Value: Identify what the customer values.
- Value Stream: Map out all steps in the process and eliminate waste.
- Flow: Ensure smooth, uninterrupted processes.
- Pull: Produce based on actual customer demand.
- Perfection: Continuously improve and strive for efficiency.
- Just-in-Time (JIT): Produce only what's needed, when it's needed, and in the right quantity
Lean thinking emphasizes a culture of continuous improvement, collaboration, and a relentless focus on customer value. It helps organizations streamline their operations, improve quality, and enhance customer satisfaction.
Systems Thinking
System thinking utilizes feedback loops; collecting information from current processes and reflecting on how to improve them.
Systems thinking is a way of making sense of the complexity of the world and your business. It’s about understanding how various elements are interconnected and how they influence outcomes. Yumpingo is a service that focuses on distilling large quantities of guest feedback into prioritized actions that will accumulate to make substantial improvements to customer satisfaction and business performance. Yumpingo enables you and your teams to see ‘patterns of change’ rather than ‘static snapshots’.
Customer-focused Thinking
All these methods require businesses and leaders to be relentlessly customer-focused. Being customer-focused is more than listening, it’s about delivering what customers need with urgency.
Upstream Thinking
Upstream thinking is a focus that emphasizes proactive problem-solving. It encourages us to look beyond immediate symptoms and delve into the underlying factors that contribute to a problem. By thinking upstream, you can create lasting solutions that prevent issues from recurring. We’ve written about this here.
To find out more about how you can implement continuous improvement with Yumpingo you can read about our Continuous Actions Process here or please get in touch with the team through the form below.
Share this:
Subscribe to our Newsletter
You May Also Like
These Related Stories
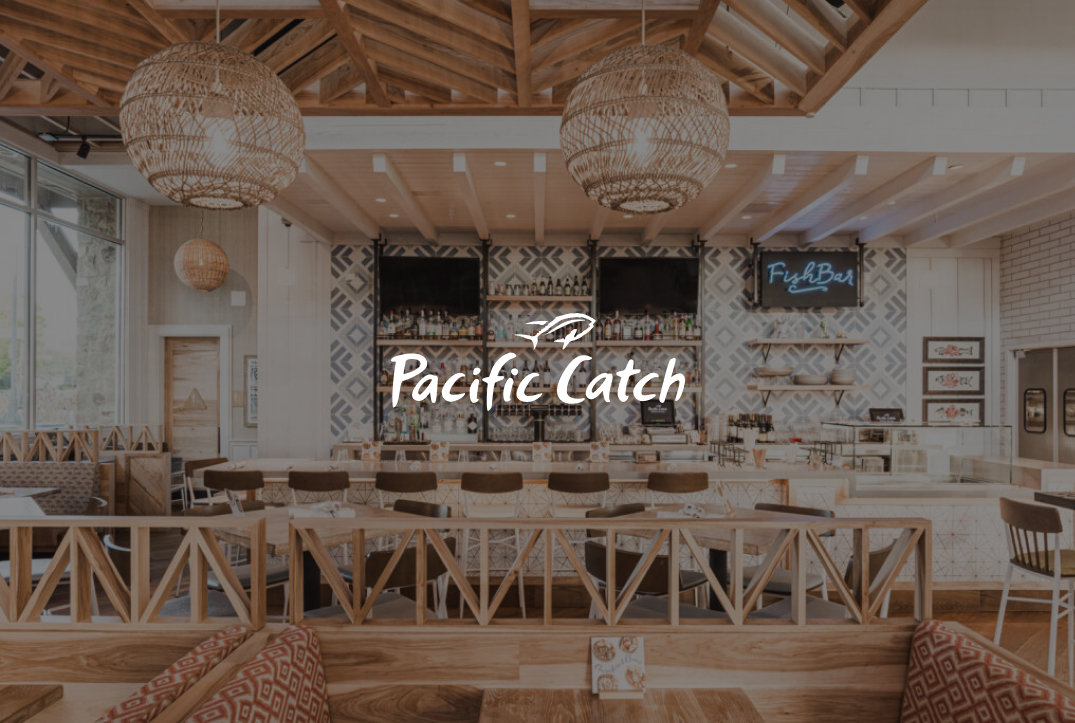
Yumpingo’s consultancy services deliver results for Pacific Catch
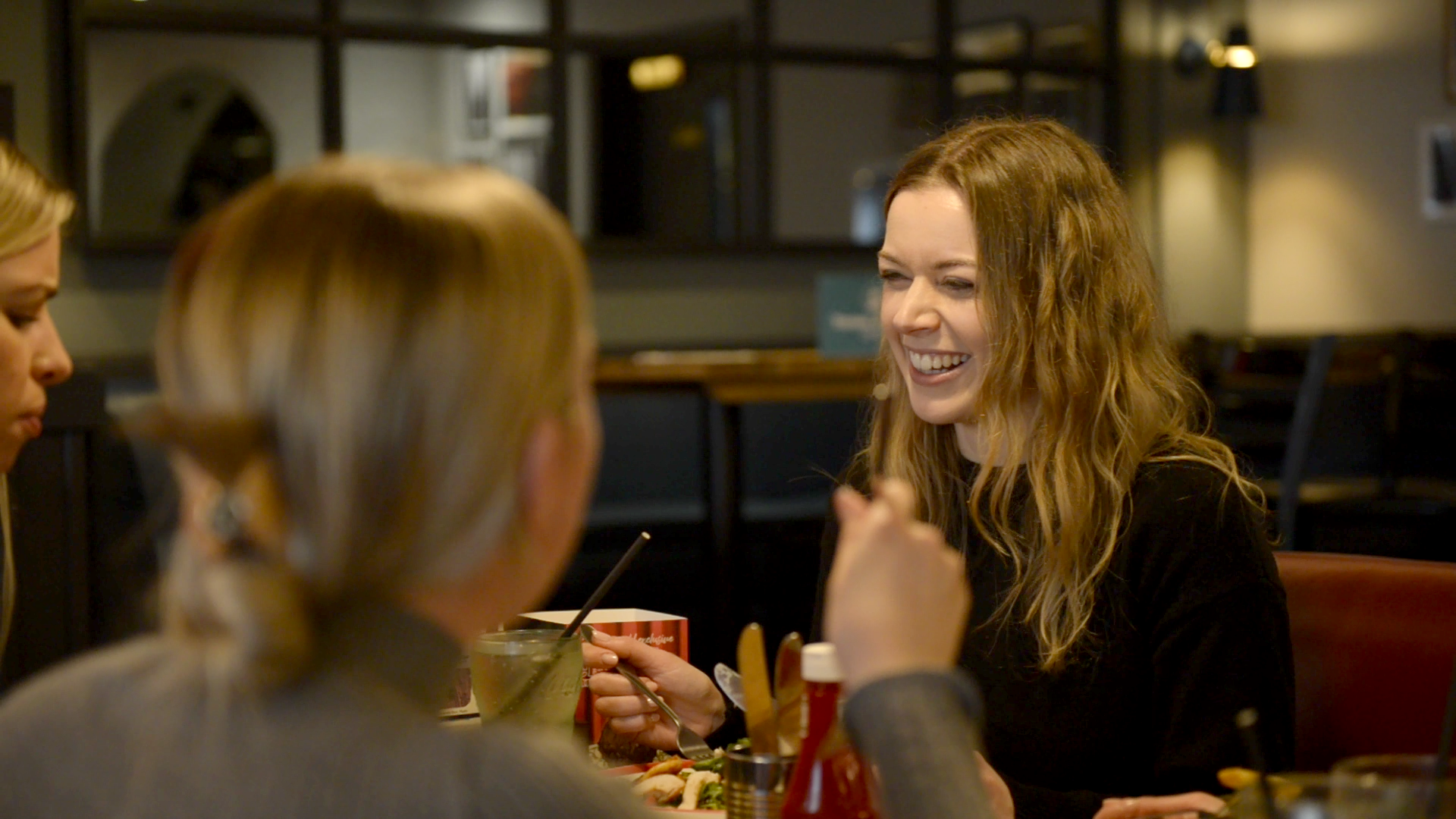
Getting ahead of the curve: Why restaurants are struggling to manage margins, and what they can do to fix it.
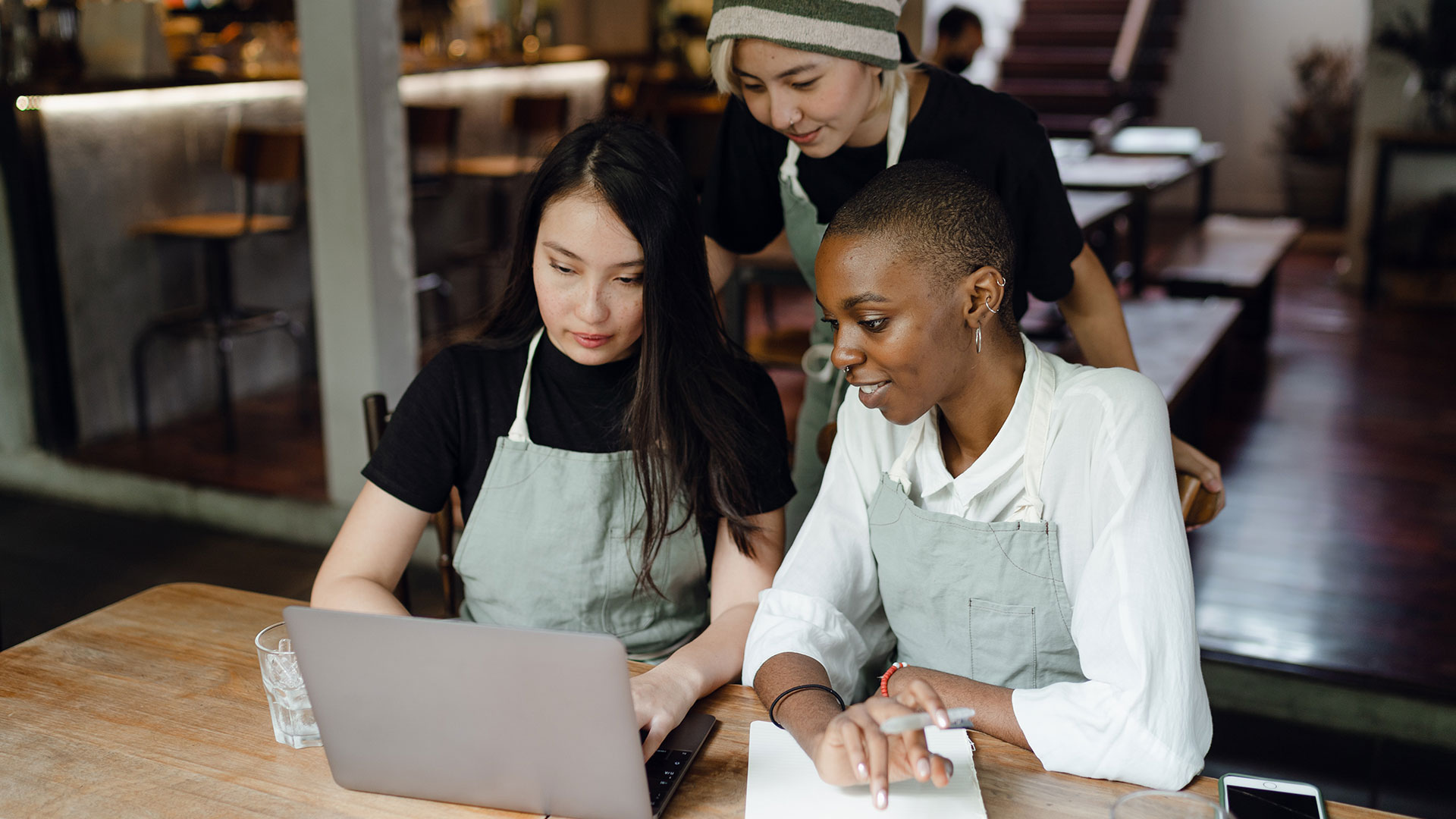